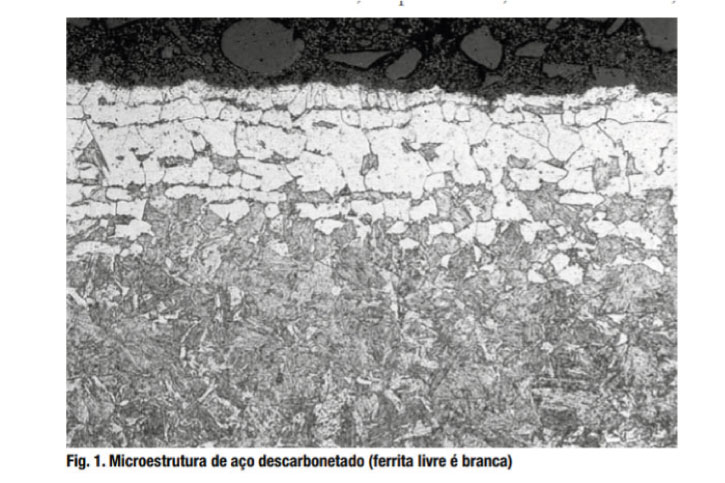
Há um grupo de perguntas recorrentes feitas ao Doutor, todas centradas em: “Quanta oxidação de superfície é permitida em uma peça de aço?” O mais recente foi um pedido inocente de “um gráfico (ou artigo) de `descarbonetação`, que mostra o efeito no aço, se normalizado, em um ambiente sem gás inerte.” O cumprimento desta solicitação fornece algumas informações valiosas para o tratador térmico. Vamos aprender mais. Embora a pergunta pareça direta, há uma série de questões importantes que surgem a partir dela, e alguma interpretação é necessária para entender completamente o que está sendo perguntado. Por exemplo, que tipo de aço está envolvido, de que forma está sendo adquirido e qual é a sequência de fabricação usada para criar as peças do componente? Do ponto de vista metalúrgico, estamos falando de descarbonetação total ou parcial? Como será medido e qual é o uso final da aplicação do produto para que uma avaliação possa ser feita do impacto da descarbonetação no design? A descarbonetação varia com o grau do material, temperabilidade, atmosfera do forno, potencial de carbono e o tipo de processo de tratamento térmico sendo realizado (por exemplo, temperatura, tempo). As peças descarbonetadas apresentam menor dureza (superficial), menor resistência ao desgaste e menor vida útil à fadiga, o que afeta sua vida útil. Um exemplo é um fabricante automotivo cujas colunas de direção estavam afrouxando na linha de montagem devido à presença de uma camada de descarbonetação parcial de 0,025 a 0,075 mm no anel de retenção do eixo. Se alguém se referir simplesmente ao AMS 2759/1 ou /2, [2,3] quatro tipos de partes são definidos que, por sua vez, ditam a classe de atmosfera permitida ou proibida ao aquecer partes acima de 677˚C. O tipo de superfície inicial (por exemplo, acabado a quente, trefilado a frio) e a quantidade de metal a ser removido por usinagem parcial ou acabada, seja maior ou menor que 0,51 mm (0,020 polegada), são os critérios importantes. Essas especificações vão além, discutindo a contaminação da superfície e fornecendo limites para itens como descarbonetação parcial, ≤ 0,13 mm (0,005 pol.) E ataque intergranular, ≤ 0,018 mm (0,0007 pol.), bem como definindo o método de medição e critérios de rejeição. Ouvir o que fazer é uma coisa, mas entender por que isso deve ser feito é outra, que era a verdadeira questão que estava sendo feita aqui.
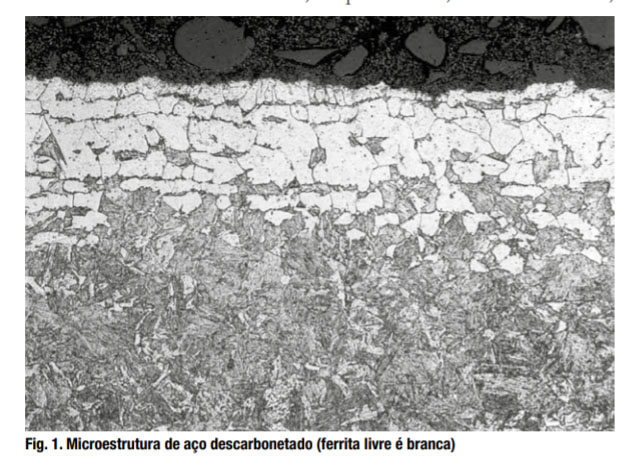
Um Pouco de Teoria [4,5] A descarbonetação total (também conhecida como descarbonetação do tipo 1) é a profundidade na qual a microestrutura da superfície é ferrita livre; ou seja, a profundidade até a qual houve 100% de perda de carbono (Fig. 1). A descarbonetação parcial (também conhecida como descarbonetação do tipo 2 ou tipo 3) é aquela profundidade da superfície onde alguma perda (maior ou menor que 50%, respectivamente) de carbono ocorreu, mas não há profundidade mensurável de descarbonetação completa. Descobriu-se que a perda de carbono da superfície próxima ocorre acima de 700˚C, quando a atmosfera da fornalha contém dióxido de carbono, vapor de água, oxigênio e hidrogênio (Fig. 2). O carbono presente no aço irá interagir com a atmosfera do forno evitados com qualquer atmosfera. A realização de testes usando um forno executando o (s) ciclo (s) de processo, no entanto, é sempre altamente recomendável para determinar os níveis reais de descarbonetação.
e sairá da superfície em fase gasosa nas condições adequadas. Isso resulta em uma mudança na concentração causando a migração de carbono do interior para a superfície, que continua até que um equilíbrio seja restabelecido, criando assim uma profundidade máxima de descarbonetação. Dependendo se o aço está entre as temperaturas crítica inferior (Ac1) e crítica superior (Ac3) ou acima da crítica superior, as taxas de difusão de carbono variam. Temperatura e composição são os principais fatores envolvidos e sua influência varia dependendo do processo (por exemplo, recozimento, normalização) sendo realizado. Um Pouco Mais Fundo [7] Como afirmado, a descarbonetação começa a ocorrer conforme a taxa de carbono na superfície diminui devido à sua reação com o oxigênio, pois essa reação excede a taxa de crescimento da formação de incrustações (óxido de ferro). A escala contribui para a profundidade de descarbonetação (por exemplo, Equação 1 sendo típica). A descarbonetação não depende apenas da presença de oxigênio, mas também da interação com outros gases oxidantes na atmosfera, principalmente o vapor d’água e o dióxido de carbono. Em um ensaio controlado, [7] as amostras foram descarbonetadas e os resultados medidos para atmosferas com baixo nível de oxigênio e ar (Tabela 1).
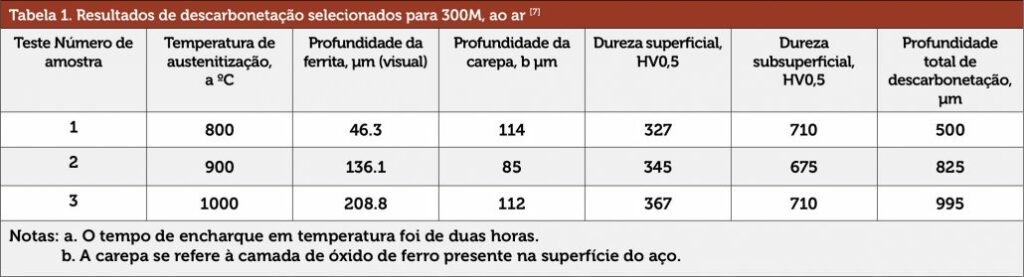
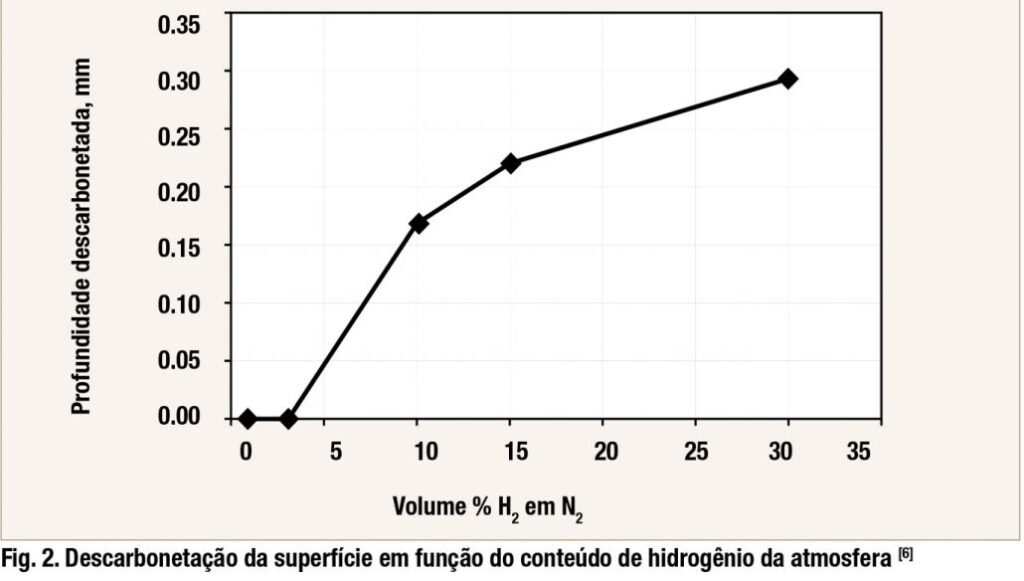
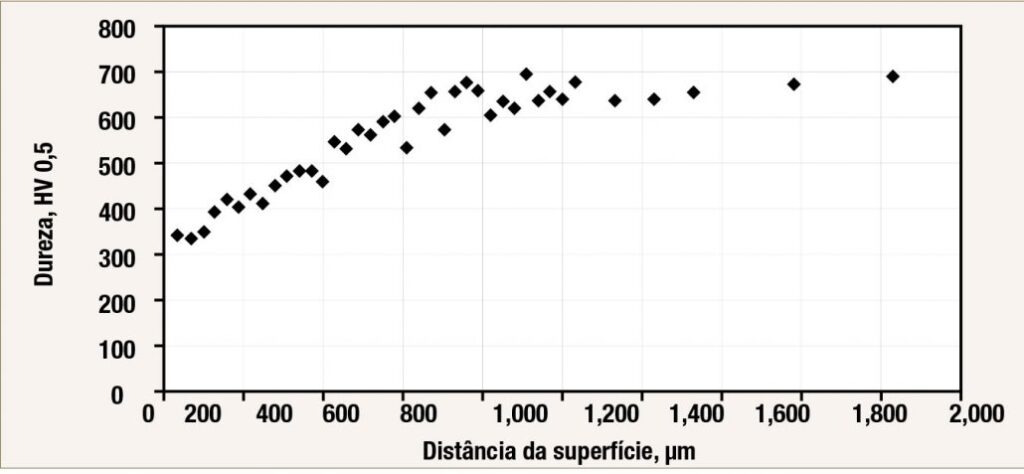
A perda de dureza foi cuidadosamente documentada (Fig. 3). Esses testes encontraram a profundidade máxima de descarbonetação em cerca de 0,51 mm (0,020 pol.), O que se correlaciona bem com as informações da AMS. FeO + CFe → Fe + CO(g) [1] Resumo A escolha da atmosfera correta do forno, temperatura e, em menor grau, o tempo em temperatura são variáveis importantes para compensar o efeito da descarbonetação. Como se viu neste caso específico, a questão envolvia a necessidade de nitrogênio como uma atmosfera de cobertura durante a normalização a 955˚C ou se o processo poderia ser feito em um forno câmara a gás com o material protegido pelos produtos da combustão. Uma vez que a remoção mínima de material foi de 1 mm (0,039 polegada) e os tempos de imersão foram de quatro horas ou menos, os efeitos deletérios da descarbonetação poderiam ser evitados com qualquer atmosfera. A realização de testes usando um forno executando o (s) ciclo (s) de processo, no entanto, é sempre altamente recomendável para determinar os níveis reais de descarbonetação.
Fonte: Texto: DANIEL H. HERRING – +1 630-834-3017- dherring@heat-treat-doctor.com –Revista Industrial Healing – Out a Dez 2020